Cultured meat: A comparison of techno-economic analyses
By Linch, Neil_Dullaghanđč @ 2021-09-24T22:20 (+165)
For cultured meat to move the needle on climate, a sequence of as-yet-unforeseen breakthroughs will still be necessary. Weâll need to train cells to behave in ways that no cells have behaved before. Weâll need to engineer bioreactors that defy widely accepted principles of chemistry and physics. Weâll need to build an entirely new nutrient supply chain using sustainable agricultural practices, inventing forms of bulk amino acid production that are cheap, precise, and safe. Investors will need to care less about money. Germs will have to more or less behave. It will be work worthy of many Nobel prizesâcertainly for science, possibly for peace. And this expensive, fragile, infinitely complex puzzle will need to come together in the next 10 years.
On the other hand, none of that could happen.
That is the takeaway from a new article by Joe Fassler (2021) in The Counter that draws heavily on two techno-economic analyses (TEA) of cultured meat (CE Delft 2021 & Humbird 2020). For full disclosure, we at Rethink Priorities were independently reviewing these TEAs (plus a third by Risner, et al. 2020) and in the process of writing a summary and comparison of them with our main takeaways.
The article addresses many of the issues we also noticed, and supplements them with interviews from industry experts. Here we want to acknowledge that they beat us to the punch somewhat, add a few relevant things we think the article left out from the comparison, and what the next steps are in our project.
The main cruxes of disagreement across the TEAs are:
- Approach to the research question
- Investor payback timelines
- Food grade versus pharmaceutical grade bioreactors
- The costs of media (growth factors and amino acids) at scale
- The limits of cell-engineering needed to reduce media consumption needs
First though, we provide our quick summaries of the three TEAs so readers have a background before diving into the comparisons.
As we are investigating a scientific question that sometimes hinges on deep technical expertise (which neither Neil nor I have), we will likely have some errors in the summaries and (especially) personal takeaways. In addition, this report is less thoroughly checked than usual for Rethink Priorities reports. It should best be viewed as our current tentative understanding of the existing literature, rather than a final definitive summary of the existing literature.
tl;dr: We reviewed 3 TEAs on cultured meat. Our summary is that Humbird is very high quality and suggests cultured meat cost-competitiveness is hard and needs everything to go right. CE Delft outlines some of what will need to go right, but doesn't provide much evidence that any of it is possible, has internal validity errors, and arguably has too much motivated reasoning. Risner, et al. is decent, within the narrow limits it sets itself, but too many details are underespecified for it to reflect the full costs and challenges of scaling up cultured meat. Reading the TEAs and doing surrounding research has turned Linch from a cultured meat optimist to being broadly pessimistic. Neil wants to be more agnostic until further research from Rethink Priorities and others.
Our TEA Summaries
As part of a project forecasting the potential for cost-competitive cultured meat to displace conventional meat, my colleague Neil and I investigated three techno-economic analyses (TEAs) estimating the economic feasibility of cost-competitive cultured meat ($2.50-$8/kg, akin to different estimates for existing wholesale meat prices).
A quick note on terms. The studies we looked at (and us) are only investigating âcultured meatâ, that is, animal cell based meat of target conventional meats (usually beef). They do not investigate other technological alternatives to conventional meats such as plant*-based meats (like Impossible Foods or Beyond Meat), fungi-based meats (like Quorn), or brain-dead/genetically happier chickens (no known products).
In addition, the studies only look at the production side of one intermediate product: that of undifferentiated animal cell slurry (70-77% water). They do not investigate the question of scaffolding (converting cell slurry into structured meat products, eg. steak or chicken wings), nor the marketing and consumer acceptance questions of whether consumers will wish to buy cultured meat if itâs widely available and cheap.
To give a quick sense of the difference between the TEAs, here are the range of prices estimated in the TEAs given various assumptions, though note the lowest estimates from Humbird (2020) and Risner, et al (2020) are not regarded as realistic by the authors.
Price estimates explored in the TEAs, USD$/kg | ||
Humbird (2020) | Risner, et al (2020) | CE Delft (2021) |
$225.03 | $437,000.00 | $22,422.00 |
$236.58 | $57,200.00 | $1,707.00 |
$36.79 | $44,500.00 | $149.00 |
$21.00 | $1.95 | $116.00 |
$17.00 | ||
$8.00 | ||
$6.52 | ||
$5.74 |
Humbird (2020)
Executive summary
Humbird (2020) presents a study (funded by Open Philanthropy) which argues that a number of very difficult scientific and engineering problems need to be solved to get cultured meat to less than $25/kg (the reference point of the more expensive end of plant-based meats), at least with production processes anywhere similar to known processes.
Humbird models an ecosystem producing 100 kilotons/year of warm-blooded mammal cell mass. He believes that after a number of difficult engineering problems are solved to get to viable cultured meat at scale, the cost of cultured meat is set by expensive capital expenditures and media costs, particularly amino acids. Ultimately, Humbird believes that significant scientific and engineering progress is necessary but insufficient for cultured meat to displace conventional meat.
The core argument is that while microbial processes (for yeast, bacteria) have scaled over decades to extremely large production volumes (and create a lower bound for attainable prices given known limits), producing animal cells at industry scale present very large challenges in comparison:
- Animal cells have a slower doubling time (24h-48h) than microbes (20min-3h)
- Practical bioreactor volume is smaller, as animal cells are less tolerant of both spatial heterogeneity (eg temperature, pH) and fixes to heterogeneity (sparging, agitation)
- Oxygen uptake/transfer rate and catabolite inhibition (lack of cell walls means harder to control osmolality) creates a limit to the practical final cell density
- Animal cells need to be fed (expensive and globally low supply of) high-quality media components, particularly near-pure amino acids.
- There are significant capital costs to maintain very high hygiene (âasepticâ) conditions, as any viral/bacterial contamination in an animal cell bioreactor is fatal.
- Significant genetic engineering is necessary to produce animal cells with the desirable properties for bioreactor use (like breaking the Hayflick limit and achieving anchorage independence)
Humbird first models a Techno-Economic Analysis (TEA) where all parameters are similar to bakerâs yeast, except for constraints imposed by the first three challenges (doubling time=24 h, maximum fermentor size=20 m3, maximum oxygen uptake rate=25 mol O2/m3-h).
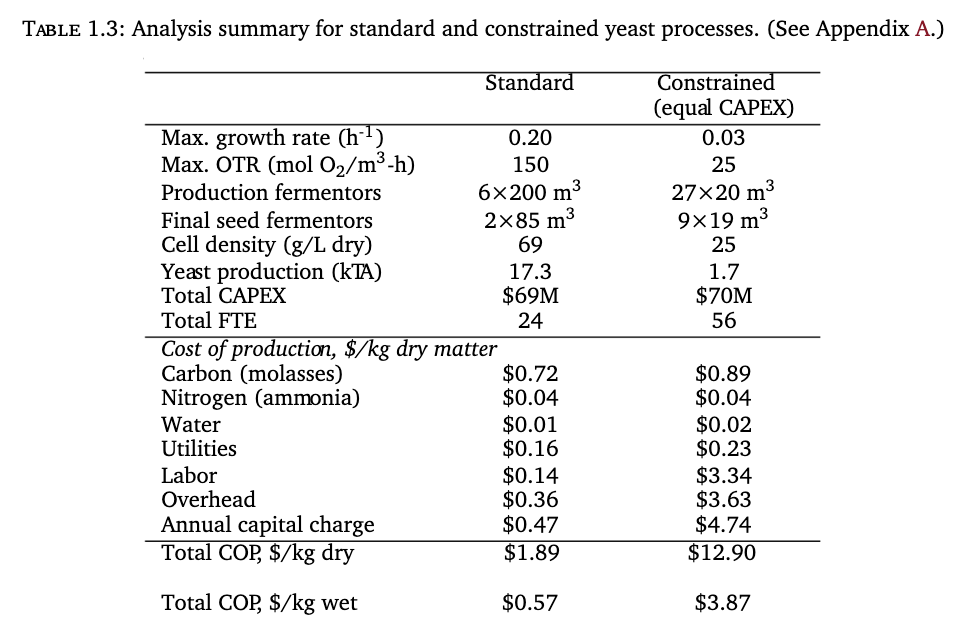
The analysis comes to $3.87/kg of wet (70% water) cell mass for the constrained yeast process. As yeast production at scale is already a highly optimized process over many decades, and the additional constraints mentioned so far are pretty close to the fundamental biological nature of animal cells, it seems unlikely that we can do better than a lower bound of $3.87/kg. Unfortunately, there are other constraints.
For the rest of the study, Humbird then considers what steps are needed for a more realistic model that incorporates all the real constraints of cellular meat, but also at prices and quantities with a large ecosystem of producers and suppliers (commensurate with a production of 100 kilotons/year), and then does sensitivity analysis on the relevant prices.
The general upshot:
- Significant metabolic engineering is necessary so enhanced cells have metabolisms at close to what Humbird believes are theoretical limits
- Cheap at scale (<$200/kg) cultured meat with âwild-typeâ cells is simply not feasible
- The cost of cultured meat is then bounded by the costs of high-quality media components, particularly near-pure amino acids, which Humbird models to be very expensive even at scale.
- Humbird speculatively considers using soy hydrolysate instead of individual amino acids in media, which will be significantly cheaper if viable.
- Secondarily, capital costs (especially but not limited to the cost of aseptic animal cell bioreactors) are also a large cost.
- In the most optimistic scenario Humbird considered (cells with enhanced metabolisms designed, soy hydrolysate absorption, all other technical problems solved), Humbird estimates a cost of $21/kg wet cell mass.
- Note that this does not include flavoring or structuring cell slurry into meat, nor does it include the amortized costs of R&D.
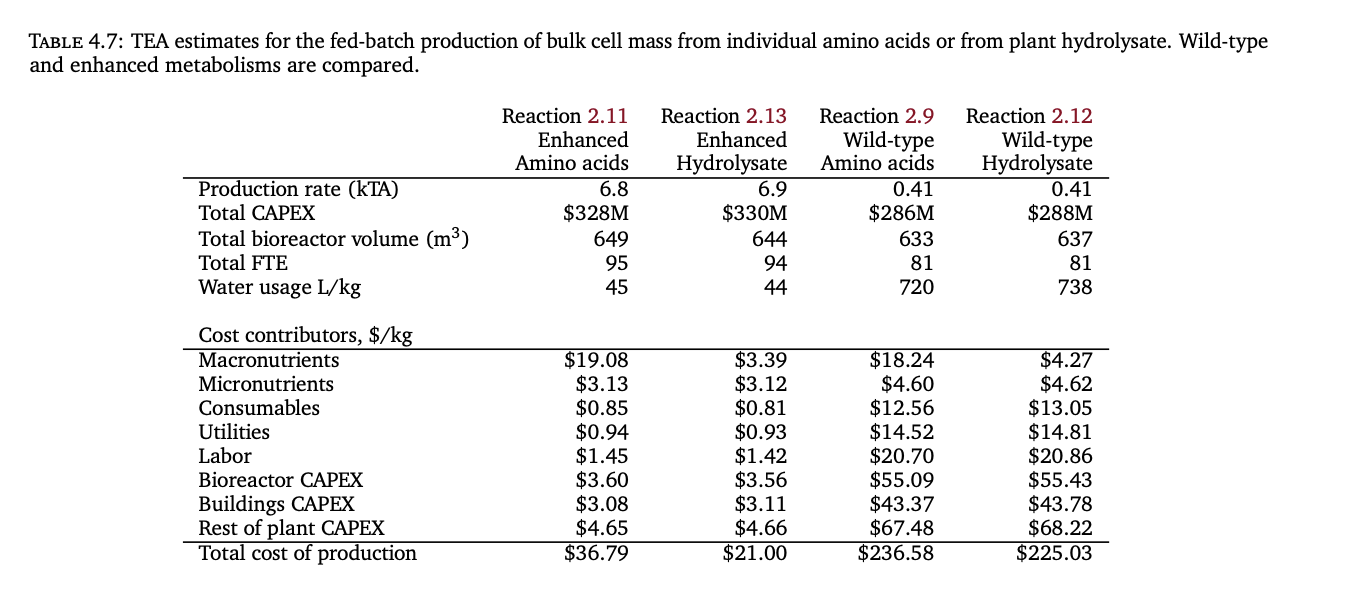
Humbird gives five key recommendations for future study. Note that in his model, solving these problems are necessary but insufficient for getting cultured meat to $21/kg.
- Cell-line engineering
- Plant protein hydrolysis
- Heat-stable media formulation
- Aseptic bioreactor design
- Nitrogen integration
CE Delft report (2021)
Executive summary
Vergeer, et. al (2021) presents a study, using both public and private data, to argue that while substantial cost reductions are necessary, they are feasible to bring cultured meat to sufficiently low cost such that we can have a large burgeoning industry of cultured (âcultivatedâ in their words) meat by 2030. This study is conducted from the consultancy CE Delft and funded by the Good Food Institute.
The core argument goes: Existing models of cultured meat via current production technology and costs for inputs will result in very expensive cultured meat. However, based on their analysis of sometimes private data from cultured meat companies, new changes just around the horizon across a wide range of avenues should be enough to cut cultured meat to fairly affordable prices, perhaps close to conventional meat baseline by 2030.
The authors model an ecosystem producing 10 kilotons/year of wet (70-77%) animal cell mass, with some intentional vagueness about which animal types they ultimately refer to. They gathered data from 16 different (cultured meat and other) companies to do this analysis. They assume food bioreactors rather than traditional animal cell bioreactors as the baseline capital cost.
CE Delft first lightly models three âbaseline scenariosâ for the expected cost of a kilogram of cultured meat, using different ranges of ingredient costs and amounts required (high is upper end, mid is geometric means of all estimates, low is lower end for everything).
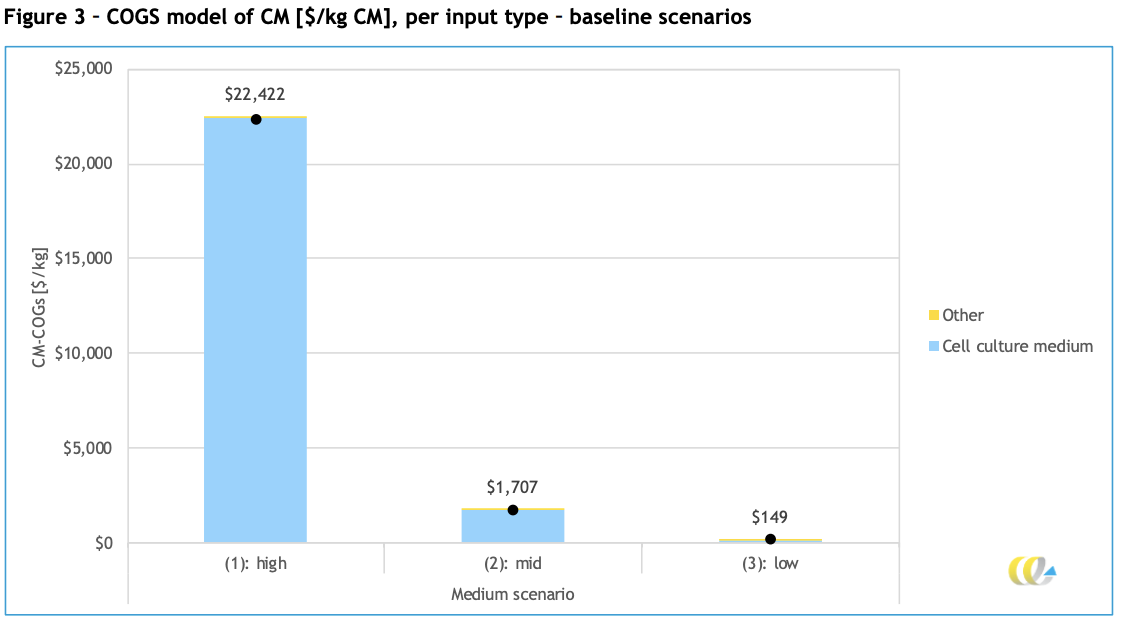
They then consider six scenarios for future cost reduction:
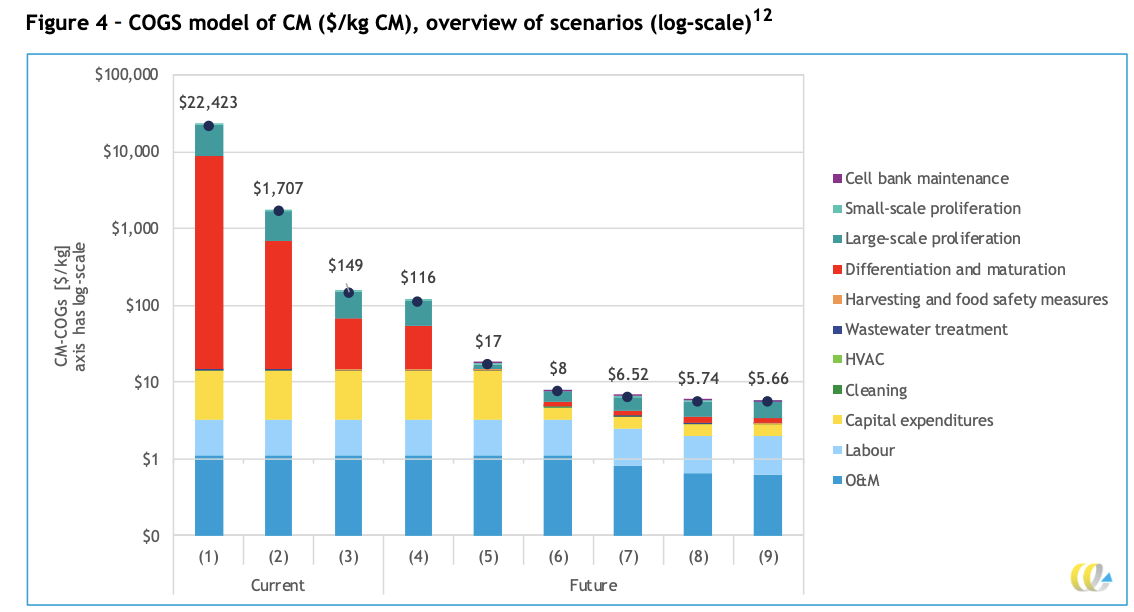
Note that scenario 4 onwards builds from scenario 3 (low end of all estimates) rather than scenario 2 (mid-range of estimates). This modeling choice is not explained.
Each scenario builds on top of the previous scenario.
- Scenario 4: Lower prices for growth factors
- âAs in other literature, we adopt the scenario that a price reduction of a factor > 1,000 may be possible. â
- Scenario 5: Cheaper or lower usage of recombinant proteins
- âWe have credible industry sources that point towards a feasible cost reduction of a factor 100.â
- Scenario 6: Capital expenditures can be repaid at a slower rate than normal
- While traditional investors require a payback time of <4 years for commercial investment projects, CE Delft argues that socially motivated investors can instead opt for a payback time of 30 years.
- Linch (For judgment calls that one of us looked into in some detail, and the other broadly agrees with but is not vetted, we specify author names in Bold so it's clearer that we're referring to just one author's opinion): It is unclear to me whether a 30 year payback time, even if true, is correctly pricing in what may presumably be higher maintenance costs, for 30+ year old equipment using novel technology.
- While traditional investors require a payback time of <4 years for commercial investment projects, CE Delft argues that socially motivated investors can instead opt for a payback time of 30 years.
- Scenario 7: Increase in maximum cell density during proliferation
- â50*106 cells/ml is the baseline cell density modeled. According to experts in the field, it may be feasible to increase cell densities by a factor 4 (to 20*107 cells/ml)â
- âHigher cell densities would mean that more meat cells can be grown in a reactor of the same volumeâ
- Though note that a factor of 4 increase in cell density means that the percentage of bioreactor volume that is now cells would increase from 17.5% to 70%, very close to sphere packing density limits.
- Scenario 8: Shortening of production run time
- âIt is estimated that a reduction in production run time of 25% is feasible.â
- Scenario 9: Increase in cell volume
- âAs the companies involved in this study produce a range of species and cell types, we used an average cell volume for the baseline scenario and determined potential larger cell volume (5,000 ”m3 ) on primary data collected and literature.â
- However, note that combining scenario 7 with scenario 9 translates to a pure cell density (% of bioreactor volume that is cells) of 100%.
Risner, et al. (2020)
Executive Summary
Risner, et al. (2020) present a study (funded by the Innovation Institute for Food and Health at UC Davis) on the costs of a 20m3 (20,000 L) food-grade core bioreactor based-system producing 121 kilotons of bovine cell wet mass (1% of current US beef production). The authors argue that âtechnological performance will need to approach [or surpass] known technical limits for animal cell based meat to achieve profitably as a commodityâ. They think cultured meat âmay not be economically viable as a commodity for some timeâ (undefined how long), but âmay enter the market place sooner as a minor ingredient which lends desirable organoleptic qualities to an otherwise plant-based productsâ or become more like luxury food items; almas beluga caviar (US$10,000/kg), Atlantic bluefin tuna (US$6,500/kg), and foie gras (US$1,232/kg).
The study employs six global sensitivity analysis algorithms of 67 parameters, chosen using cellular biology and chemical/process engineering conventions. The list is narrowed down to the nine factors that most influenced capital and annual operating expenses by consolidating the top five parameters across all six algorithms:
- Average single cell volume
- Average single cell density
- Fibroblast growth factor-2 (FGF-2) concentration
- FGF-2 cost
- Glucose concentration
- Glucose consumption rate per cell
- Maturation time
- Transforming growth factor beta TGF-b (a growth factor) concentration
- Oxygen consumption per cell
In the paper itself the authors don't spend much time discussing TGF-b or oxygen consumption per cell, despite TGF-b being a major cost variable and oxygen uptake rates being a major obstacle in Humbirdâs TEA. Their interactive cost calculator illustrates that media/recombinant protein costs also substantially affect cost (especially transferrin, L-Ascorbic acid 2-phosphate, and insulin). Furthermore, they also cite bioreactor capital costs as a significant factor in costs, even after assuming food-grade bioreactors.
These nine factors were then clustered into technological components. Four technology development scenarios are then developed, based on altering the values of some of these nine variables (see table below). The four technology development scenarios are:
- Scenario 1 US$437,000 per kg : baseline scenario based on existing animal cell based meat production, in a food-grade bioreactor, including 2019 pricing (obtained from a GFIâs Specht (2019) for animal serum-free media and growth factors, and reported human embryonic stem cellsâ glucose uptake rates.
- Scenario 2 US$57,200 per kg: halves the cost of growth factors, reduces cell doubling time from 24hrs to 16hrs, halves glucose consumption rate per cell, increases total cell volume density 5x - based on 2x108 cells/ml average max cell density, which the authors note is a physical limit and the number in reality would be much lower.
- Scenario 3 US$44,500 per kg: Same as scenario 2 but eliminates the cost of growth factors.
- Scenario 4 US$1.95 per kg: An intentionally pie-in-the-sky scenario was designed to see what it would take to reach ~$2/kg (for conventional beef price parity). Nearly all technical challenges are resolved, including reducing growth factor costs to zero, increasing myoblasts/myosatellite cells (MSC) tolerance to glucose concentrations, glucose/media consumption is reduced by an order of magnitude, halving again myoblast/MSC doubling time and lower maturation time 6x, reducing media/recombinant proteins costs (base media containing over 50 ingredients, TGF-b, transferrin, L-Ascorbic acid 2-phosphate, and Insulin) to zero, and increasing total volume density to 100% (which is biologically implausible but unlike CE Delft (2021), Risner, et al (2020) acknowledge this).
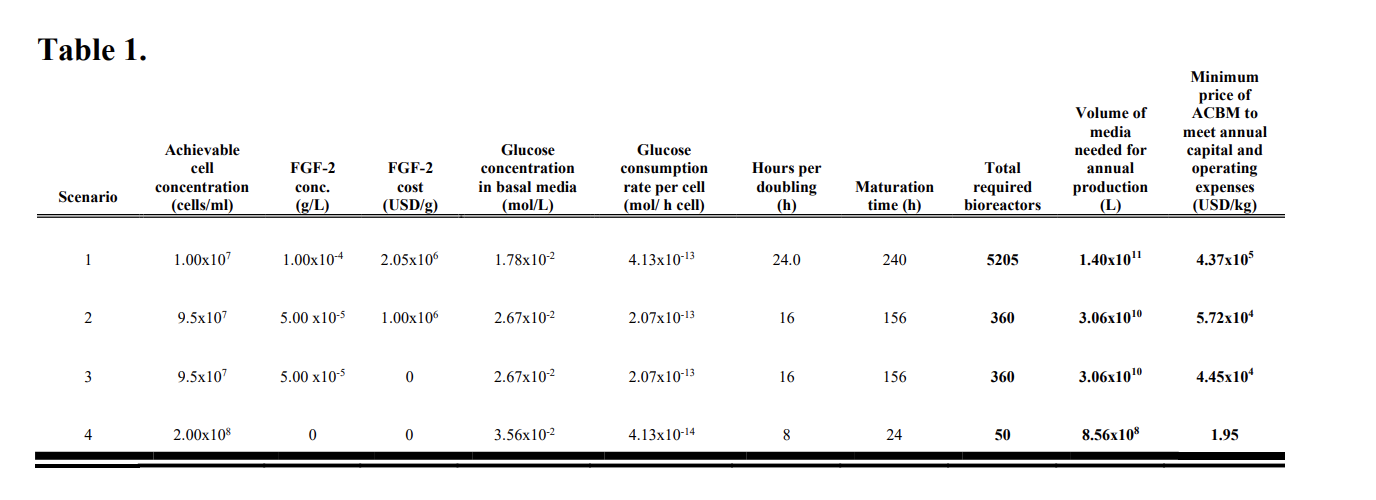
- Note that this TEA modelled only the core bioreactor system costs, as if every other part of the process was free, so is intended as a minimum cost.
The key three recommendations of the paper in order to lower costs are:
- cell selection/engineering to lower the media consumption rate via a more glucose-efficient metabolism
- âEngineering and/or screening for cell lines which shift rapidly from a Warburg metabolism (aerobic glycolysis) to a more glucose-efficient metabolism (oxidative phosphorylation i.e. production of 2 ATP vs. a theoretical 38 ATP per glucose molecule)â: from 4.13*10-13 moh/h cell glucose consumption rate per cell to 4.13*10-14 moh/h cell. Note that their argument is less about glucose specifically, which after all is just a simple sugar, and more about using it as a proxy for total media consumption requirements and thus a measure of cell-engineering.
- reducing or eliminating the cost of growth factors (especially Fibroblast growth factor-2)
- They suggest one way to eliminate FGF-2 costs is by âleveraging the ability of cancer cells to increase glucose uptake rates and exhibit cell proliferation without the presence of growth factors, or cell lines could be engineered/identified to express oncogenes related to these traits.â However, they note this âcould be challenging from both a regulatory perspective as well as for consumer acceptance.â
- scaling up of perfusion bioreactors.
- Doing so allows for multiple changes of media per batch and higher cell concentrations. However, the TEAâs costs are based on estimates for standard food-grade bioreactors and Risner, et al. (2020) acknowledge more sophisticated bioreactors (i.e. single-use or novel perfusion systems) may substantially increase capital costs.
- An implicit fourth recommendation is also to substantially lower the costs of the media/amino acids used.
- âThe amino acids being a big variable in the cost calculation assumes that there has been a solution for the other expensive components like growth factorsâ (private correspondence) . . .âOur model did not account for amino acid uptake rates due to glucose being the most consumed nutrient in cell culture, however amino acid (AA) metabolism should be a consideration for commercial scale up" (supplementary material, p2)
Why do the TEAs disagree?
Overall approach of the TEAs
- Humbird asks, if cultured meat scaled to a global volume of 100 kilotons per year, what would it cost? CE Delft imagines a world where 10,000 metric tons per year of cost-competitive cultured meat can be produced, and then reverse engineers what would need to change for that to happen (unrelated to how likely those changes are). Risner, et al. (2020) follow a similar model to Humbird and then explore what changes to the major cost factors would be needed to get to price parity (acknowledging that they are unlikely).
- Our takeaways on the TEAs overall:
- Linch: My general impression is that Humbirdâs analysis was very carefully and rigorously done (though I wish his uncertainty was sometimes made more numeric, as from an EA perspective many of these investments are worth doing even if thereâs only a 5-20% chance of cultured meat working out in a thirty year time horizon). In contrast, my impression is that both the CE Delft report and its subsequent heavy publicity can best be viewed as a textbook exercise in motivated reasoning (akin to this, but less subtle). Various decision points and errors in the report shade in favor of cultured meat being cheap/quickly viable, likely without corresponding errors in the opposite direction. I have not read Risner et.al as carefully as Neil and feel less qualified to opine on it. My understanding is that Risner concludes cost-competitive cultured meat is impossible at current technology, but has an explicit âthis is where a miracle happensâ final step where you get very cheap prices if you assume away all technical and engineering difficulties. Note that I do not have prior experience in either this field or adjacent fields, and am biasing towards overexplaining and communicating my current opinions instead of only saying things Iâm certain is true.
- Neil: To me the major distinction between the TEAs is what reference class they are using for technological breakthroughs. Humbird (2020) and Risner, et al. (2020) seem to imagine the correct reference class is one with real technological and cost limits, like biofuels, while CE Delftâs (2021) view is closer to reference classes where the technical challenges can be overcome with enough effort/support from researchers, investors, and government, like photovoltaic technology (solar panels). None of the TEAs provide a useful way to adjudicate if itâs possible to beat the amino acid prices the yeast industry has achieved or to design bioreactor systems that can reduce the costs of contamination at scale, but I think CE Delft (2021) undersells just how much effort is needed. I also found it concerning for the CE Delft (2021) TEA that Linch was able to spot a fundamental mathematical/conceptual error without any prior domain expertise. These are the only TEAs Iâve read so I donât have a good sense where they fall on the quality scale of TEAs in general. The TEAs should just be one (important) part of your model on how likely cultured meat is to scale.
Investor timelines
- In brief, Humbird thinks it would take at least 60 years for the required ten orders of magnitude manufacturing cost reductions to be achieved via normal economies of scale, and investors work on much shorter timelines with higher return expectations for the first successful plant. CE Delft argues cultured meat investors are a special socially motivated breed that will wait 30 years for their returns.
- Humbird (2020) simply doesn't believe a scale up can be achieved in any reasonable investor timeline. He argues that a scale up to conventional meat volume, on the order of 100M metric tonnes/year, requires a ten orders of magnitude increase from the production volume of edible cultured animal cells at the time- on the order of 1â10 kg/y. He argues (2020, p9-10) it took 60 years for âcertain aspects of computing to have progressed by about ten orders of magnitudeâ, and âgenerally accepted economies of scale in the process industries do not hold within them multiple orders of magnitude in manufacturing cost reductionâ . Therefore, âto fit this many powers of ten into a time scale that meets contemporary investor expectations, some would suggest that even more accelerationist âlawsâ are in play for cultured meatâ. Humbird (2020, p11) argues cultivated meat optimists are following a reasoning of âCAPEX only matters for the first plant; all subsequent plants will be financed at a low cost of capitalâ but that âsuch treatment from lenders is, more accurately, only enjoyed after the first successful plant. This need to reconcile a sense of urgency with a reluctance to be âfirstâ was an exceedingly common source of friction in the days of venture-backed biofuels startupsâ.
- Humbird (2020, p10) also seems concerned that limits to multiple orders of magnitude progress is especially true âin biotechnology, where the equipment in question is much smaller and more specialized and where the precursor chemicals are only produced in limited quantitiesâ. This is based on Humbirdâs conclusion that pharma-grade safety standards will always be required and amino acid costs will be high even at scale, both of which seem more malleable to us than Humbird claims.
- CE Delft (2021, p21) writes âtypically, the hurdle for commercial investment projects to get funded is payback time < 4 yearâ but argue socially motivated investors are willing to wait longer for returns. The authors think the payback time should be 30 years. This drops the price from $17/kg to $7.74/kg.
- However, itâs unclear why 30 years is actually justified or why socially motivated investors would prefer much longer payback time relative to normal investment that will get you more resources to use for donation or social investment later.
- Linch: I also think that CE Delftâs (2021) assumption that maintenance costs are a flat 5% of costs is suspicious/insufficiently defended.
- Linch: while itâs possible Iâm misunderstanding, a huge related issue with having a capital expenditure investment that takes >30 years to pay off is that you are explicitly baking in not changing capital use (much) which means youâre planning to keep old equipment, which seems especially wild when âold equipmentâ is decomposed into specific items like âbioreactors in a new field like cultured meat.â So I think that the CE Delft assumption about socially motivated investor attitudes is both by itself dubious but also their conclusion is invalid given just that assumption.
Food versus pharma grade bioreactors
- Humbird (2020) thinks that cell cultures cannot be manufactured at large scale using food-grade standards because cell contamination will destroy the product. Therefore, cultured meat is limited to smaller scale pharma-grade standards with virtually no contamination, which are very costly. CE Delft (2021) imagines a world where it will be possible for cell cultures to be produced in food-grade bioreactors. Risner, et al. (2020) allow for the âoptimistic assumptionâ that advances in science will enable production using food-grade bioreactor systems, and that âoperational issues related to bioreactor sanitation and fill rates are negligibleâ.
- For Risner, et al. (2020) âcost estimates of food-grade bioreactors were calculated using a method which accounts for equipment scaling, installation, and inflation. This method applies a set unit cost of $50,000/m-3 for a food grade bioreactor and a common scaling factor of 0.6â, and a capital cost of $778K for a 20K L bioreactor. CE Delft (2012) rely on more perfusion bioreactors in their model at $600K a piece, but their 10K L stirred-tank bioreactors are suggested to cost $325K a piece. Humbirdâs pharma-grade bioreactor costs are as much as an order of magnitude more expensive.
- Linch: Note that in the CE Delft (2021) and Risner, et al. (2020) reports, using food-grade bioreactors is an assumption of the models, not a conclusion. In contrast, Humbird (2020) spends ~3 pages of his report explaining the modeling choice of pharma-grade reactors and why he believes those are more appropriate.
- Neil: Humbirdâs (2020) model assumes that pharma-grade is needed to avoid contamination. Itâs unclear to us what percentage of a production batch could be spoiled and still be profitable for cultured meat companies. It may be higher than what pharmaceutical companies would accept. Fasslerâs (2021) article suggests that a single particle on a glove or a poor weld on a piece of equipment is enough to contaminate the batch and would take hours to resolve.
Media/growth factors
- Fassler (2021) points out that fetal bovine serum-free media is expensive and challenging to create. Here Humbird (2020) is more optimistic, thinking falling prices are possible with economies of scale and growth factors wonât be needed in high concentrations anyway. CE Delft (2021) also projects growth factor costs falling but still regards them as a big hurdle. Risner, et al. (2020) think Essential 8, an animal free growth medium, does not seem like a viable option and growth factor costs need to be completely eliminated.
- There is a large discrepancy between the costs for transforming growth factor beta (TGF-b). While Risner, et al. (2020) cites a study from GFIâs Liz Specht (2019) and a cost of $80.9M/gram from it, CE Delft cites an online market Qkine and that same paper from Specht but arrive at a range of $3.7M-$5M/gram for their baseline scenario. Spechtâs paper also includes a cost for a hypothetical 20,000 liter batch of $3.2M, which is perhaps what CE Delft used. Humbird assumes two orders of magnitude cheaper costs are possible.
- While this is not explicitly stated in any of the analyses, we think (following Humbird) thereâs a reasonable argument that growth factors only need to be cheap for cultured meat, so not much prior research or optimization power has been spent on making growth factors cheap historically, so we should be much more optimistic about revolutionary change being possible here over eg.cheaper amino acids or bioreactors or changing the rate that animal cells double.
- Weâve also talked to a few people working in adjacent fields who thought that massively cheaper growth factors were plausible, but none of them were very knowledgeable or confident about this area.
Costs ($/g) | Ce Delft:Baseline | Risner, et al (Scenario 4 to Scenario 1) | Humbird |
Insulin | 155-400 | 0-340 | 7-9 |
Transferrin | 246-400 | 0-400 | 12-15 |
FGF2 | 1.3M-2.3M | 0-1M-2.1M | 69-812 |
TGF-ÎČ | 3.7M-5M | 0-80.9M | 18,837-24,000 |
Amino Acids
- The viability of inexpensive amino acids is a major source of contention between the TEAs. Humbird (2020) thinks if cheaper amino acids were possible they would have been achieved already for the yeast industry. Risner, et al. (2020) also think amino acids are a huge prohibitive expense, but don't discuss them in detail because they view growth factors as an obstacle that needs to be tackled before one can even think about amino acid costs. CE Delft (2021) uses a baseline price estimate for an amino acid product that would be poorly suited to cultured meat production as a feasible lower bound for prices.
- Humbirdâs (2020) best case model using enhanced hydrolysates says that macronutrients, i.e. amino acids, could reach $3.39/kg. Risner, et al. (2020) models the base media, which includes the amino acids, as costing $0.24-$3.12/L. CE Delft (2021) project amino acids from hydrolysate can be scaled to cost as little as $0.40/kg.
- Fassler (2021) writes âWhy the discrepancy? A footnote in the CE Delft report makes it clear: the price figures for macronutrients are largely based on a specific amino acid protein powder that sells for $400 a ton on the sprawling e-commerce marketplace Alibaba.com. That source, though, is not likely not suitable for cell culture. Via a chat tool, I asked the Alibaba vendor if the product would be acceptable for use in pharmaceutical-grade applications. âDear,â she wrote back, âitâs organic fertilizer.â (In other words, it would not be.) As described on the webpage, the product is intended to be used in crop irrigation systems to help with plant nutrient uptake. The vendor did confirm it would be appropriate to use as an additive in livestock feed.â Fassler (2021) notes that ânutrition sources like the one sold on Alibaba will probably never workâ: theyâre not intended for human consumption, they may include heavy metals, arsenic, organic toxins, and so on which will get into the cells.
- According to Humbird (2020), today's production of certain amino acids would need to increase 6x to meet the demands of cultured meat, which he thinks is not going to happen. Humbird (2020) does explore the possibility that companies could derive a full amino acid profile from cheap commodity soy, reducing costs dramatically, however this would take years of research and a large scale up in the industry providing it
- CE Delft (2021) is more optimistic about both alternatives like (soy) hydrolysate and lower grade conventional production of amino acids than Humbird (2020) is, meaning you donât need to purchase expensive pure amino acids.
- Individual amino acid costs donât factor into Risner, et alâs (2020) written analysis mostly because they think the amino acids being a big variable in the cost calculation assumes that there has been a solution for the other expensive components like growth factors. The authors acknowledge that amino acid metabolism should be a consideration for commercial scale up. Their model does use a range of $0.24-$3.12/L for the base media which includes amino acids. These costs come from Specht (2019, p14). The actual range goes up to $376/L but Risner, et al (2020) only use the costs under conditions when growth factor requirements have been reduced and are produced at larger scales and higher efficiency. Itâs also worth noting that p16 of this Agronomics slidedeck citing Specht (2019) includes a âcurrentâ media price of $10/L.
- While Humbirdâs (2020) take on amino acids is the most careful one so far, it is far from obviously correct. He curve-fits a regression model of existing amino acid volume: price pairs to the new âcultured meatâ grade formulations, but some of the resulting prices are well above existing market rates for specific amino acids (human-supplement grade glycine can be bought at small scales for $27/kg from Amazon, considerably less than Humbird's (2020, pg41) $87/kg estimates.).The synthetic biologists we talked to thought that revolutionary changes in amino acid production were not obviously implausible.
- However, even if just one core amino acid at sufficiently high purity is too expensive, this may be enough to doom the entire project. At scale, amino acid prices can be lower than existing prices (as at-volume production is cheaper), but they can also be higher because the quality grade/purity needed is higher. For example, L-threonine (Thr), is currently produced at scale but using E.coli, meaning it needs to be filtered to be safe for consumption. Whether cheaper livestock-grade amino acids could be used is a testable hypothesis for cultured meat engineers.
- Some more thoughts here.
Cell engineering
- According to Fassler (2021), âthe cell density issue is one of the most intractable problems this emerging industry will face. Considering that the pharmaceutical industry has already likely spent billions on this very challengeâsums that make the total investment seen in cell meat look like a drop in the bucketâsolving it would be a stunning accomplishment.â
- As Humbird (2020) notes, talking about biological âmax cell densityâ and âaverage cell volumeâ hides the actual issue that only so much of a bioreactorâs volume could be filled by cells. Humbird argues (citing some Chinese Hamster Ovary cell studies) that the practical upper bound for volume density is 25%.
- In contrast, CE Delft (2021) starts with a volume density of 17.5% (below Humbirdâs limit), but quickly goes on to
- In a middle scenario, increasing max cell density by 4x, getting to a volume density of 70%, not only hitting way above Humbirdâs practical upper bound but also coming dangerously close to the theoretical sphere packing limit.
- In the final scenario, CE Delft increases the âAverage cell volumeâ by almost 50%, from 3.5 x 103 ”m3 to 5.0 x 103 ”m3.
- Unfortunately, they chained the two scenarios, implicitly claiming a 100% volume density (in other words, the entire bioreactor has only cells).
- This is biologically/physically implausible as
- There is no way for resources to get to cells if thereâs no nutrient solution in the tanks
- Animal cells are not perfect cubes
- Weâve informed CE Delft of this error.
- Thus, the qualitative take from Fassler (2021), that CE Deflt's (2021) numbers are unrealistic, rather than essentially physically impossible, is arguably still too optimistic about CE Delftâs (2021) perspective here.
- Risner, et al. (2020) repeats this 100% cell density implausibility intentionally in their all-problems-resolved scenario 4. âThis was done to basically account for any innovation in vascularization and fusing of the cellsâ (supplementary material, p2). They recognise it is definitely biologically implausible and nearly physically impossible. Their use of 9.50E+07 max Cell density (cells/ml) was simply a midpoint between scenarios 1 and 4 and didnât try to take into account Humbirdâs suggested practical upper limit.
Max Cell density (cells/ml) | Average Cell volume (”m^3) | Total cell volume | Volume density | |
CE Delft lower limit | 5.00E+07 | 3.50E+03 | 1.75E+11 | 17.5% |
CE Delft upper limit | 2.00E+08 | 5.00E+03 | 1.00E+12 | 100% |
Humbird upper limit | 5.00E+07 | 5.00E+03 | 2.50E+11 | 25% |
Risner lower limit | 1.00E+07 | 5.00E+03 | 5.00E+10 | 5% |
Risner middle limit | 9.50E+07 | 5.00E+03 | 4.75E+11 | 47.5% |
Risner upper limit | 2.00E+08 | 5.00E+03 | 1.00E+12 | 100% |
- Humbird (2020) takes the example of Chinese hamster ovary cells - immortal, non-cancerous, and morphologically stable cells that âcan be grown in high-density cultureâ and ârequire only a limited number of growth factors, making it possible (though still challenging) to design cost-optimized, serum-free mediaâ (Humbird 2020, p13). This particular cell line âwhich has benefitted from more than 60 years of constant research and developmentâis âprobably not efficient enough for low-cost production of bulk cell mass,â according to Humbird in Fasslerâs (2021) article. âThe chemical reactions occurring inside a living cell proceed with the usual thermodynamic efficiency of 30â80%. If an organism lives at all, it does not do so orders of magnitude away from its physical limitsâ (Humbird 2020, p9).
- Risner, et al. (2020) starts with human embryonic stem cells likely exhibiting a Warburg metabolism (aerobic glycolysis) glucose uptake rate of 4.13*10-13 moh/h but argue cell-engineering is needed to change to a more efficient oxidative phosphorylation metabolism to allow a rate as low as 4.13*10-14 moh/h, even after eliminating growth factor and amino acid costs completely.
- Neil: Glucose specific metrics are used as a proxy for overall media consumption requirements as it is the most consumed nutrient in cell culture. We toyed around with their interactive online model. Moving glucose concentration and consumption rates to the limits allowed in their model (beyond those used in their scenarios and beyond known demonstrated limits as far as I can tell), the price is still prohibitively expensive when media costs are not reduced. Taking scenario 3 and removing other media costs but keeping the preset glucose variables holds the price above $60/kg. Itâs unclear whether glucose consumption metrics are a good proxy for overall media consumption requirements.
- Humbird (2020) and Risner, et al. (2020) also mentions other critical (but presumably solvable) scientific challenges to getting cultured meat at scale, including producing immortal cell lines breaking the Hayflick limit and cells that donât automatically adhere to the sides of tanks (which animal cells are wont to do).
Concluding thoughts
This post is part of a project that aims to come up with concrete forecasts and opinions about the likelihood and timelines of cultured meat technology. The publication of existing cultured meat industry predictions and this summary of TEAs was expedited by articles in the media doing much of the same work. The next step in the project moves into forecasting. We intend to produce our own forecasts on cultured meat timelines, taking into account relevant reference classes, the TEAs, expert outreach, and our own analysis.
As this is both an important topic and a highly technical one where we do not have prior experience, we also plan to hire external experts to red-team our analysis and check for relevant flaws post-publication.
Acknowledgements
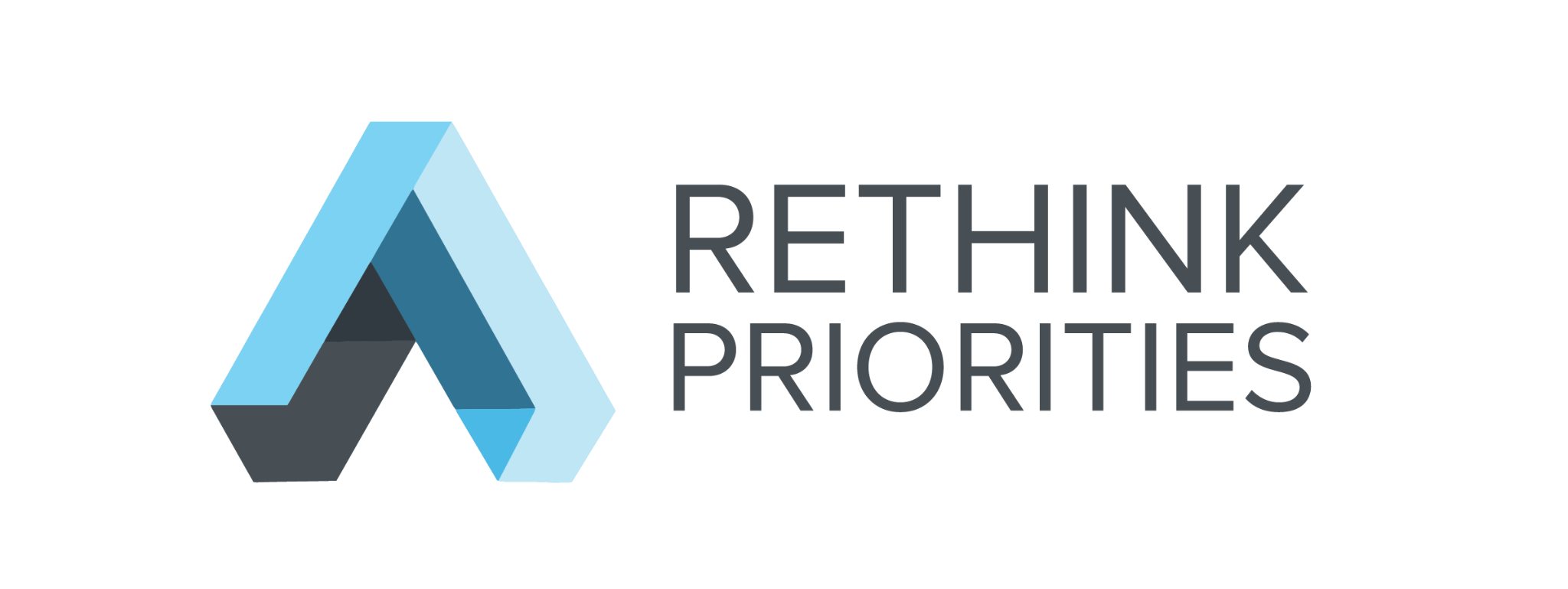
This research is a project of Rethink Priorities. It was jointly written by Neil Dullaghan and Linch Zhang. Thanks to Peter Wildeford and Marcus A. Davis for helpful feedback. Thanks also to everybody who responded to our emails and social media inquiries, including the TEA authors and relevant experts. If you like our work, please consider subscribing to our newsletter. You can see more of our work here.
Matthew Stork @ 2021-10-05T20:21 (+13)
Hey all, I've got some thoughts here. I worked in biopharma and spent some time working on a high-cell density perfusion system with CHO cells, so I've got some unique insight here. Right now for biologics production, there is a ton of effort in developing medium-scale perfusion processes run in single-use bioreactors (i.e. plastic bags). None of the analyses focused on this mode of production. There are potentially massive benefits to this approach.
- Single-use equipment solves the sterility issue. Single-use equipment can be pre-assembled and sterilized in place. This allows for plants that don't maintain strict sterility, saving on capital costs and operational costs. Note that this is not standard right now; biopharma plants with single-use equipment still usually maintain high air quality. However, for food-grade applications I bet you could get away without high quality air if you relied on single-use equipment.
- There are massively reduced capital costs when using single-use equipment. I've heard that single-use bioreactors (SUBs) can cut CAPEX by ~70% or so, although I imagine these numbers are inflated by companies advertising the sale of SUBs. Still, this puts us much closer to a reasonable cost. Of course, this is offset somewhat by the cost of the bags. However, with a sufficiently long perfusion culture (maybe say 60 days), you can cut the amount of single-use materials required. You also save on cleaning costs, as you can dispose of single-use equipment after use. There is potentially a higher labor cost here, as you will need labor to remove old equipment and install new equipment between runs. This is likely offset somewhat by less labor cost for cleaning.
- Humbird suggests using ATF membranes for cell separation in perfusion, which is incredibly expensive (10% of the cost in his optimistic scenario). ATF and other membranes are the standard separation method for biopharma perfusion right now, but there are potentially better methods out there. Stuff like acoustic wave settling or Hydrocyclones could be significantly cheaper (full disclosure, I contributed in a small way to this hydrocyclone work).
- Spent media could be purified to recover and recycle any micronutrients. Macronutrient recovery would be harder, but is still potentially feasible. (To be fair, you could do this with any approach, but it's worth nothing)
The main downside is that right now SUBs are limited to ~2,000L. There are bags as large as 6000L out there, although I have no experience with them. However, in general the use of SUBs is relatively new in biopharma, so I expect there is still ample room for scale-up. In any case, this approach would likely require a larger number of smaller perfusion reactors running in parallel.
I'm generally skeptical of the assertion that this will require "Nobel Prize winning" efforts to fix this. Honestly, sterility seems like the hardest problem of the bunch to me, which is why single-use materials seems like a winner. My gut tells me that it really shouldn't be that hard to get cheap amino acids from soy; this isn't based on a careful analysis mind you, it just really seems like this would be solvable if scaled-up sufficiently.
Dave Humbird @ 2021-11-17T01:53 (+19)
Single-use technology (SUT) in biopharmaceutical manufacture offloads many risks associated with upstream cell culture farther upstream--to media suppliers etc. A producer with a full-SUT process does not even carry the risk of cleaning and maintaining their own equipment. The purported economic and environmental benefits of SUT are related to the elimination of sterilization steam (because everything is gamma-sterilized before shipping) and the elimination of cleaning chemicals (because the bags are not cleaned for reuse).
The size limit of 2,000 L arises from the mode of sterilization--the penetration depth of gamma radiation from a cobalt-60 source is about 30 cm. In a stirred-tank configuration, this means that the rigid impeller inside the bag can be no larger than ~50 cm in diameter when the bag is folded up and irradiated from two sides. Following typical bioreactor geometry rules for animal cell culture (vessel height/diameter ratio and vessel/impeller diameter ratio), a 50-cm impeller indeed limits the scale to 2,000 L. For typical microbial bioreactor guidelines (very high OUR), the SUT limit is rather closer to 1,000 L. The 6,000 L bags are meant for very low cell density processes (very low OUR), like vaccine production in Vero cells on microcarriers. An alternate SUT configuration is the wave bag; the largest out there today is also 2,000 L (looks like a queen-size water bed) with a 50% working volume.
From my perspective, the SUT argument got too tortured between the small maximum size, the amount of waste generated (including daily media-prep bags, filters, and hoses), the observation that large stirred bags still need to sit in a permanent stainless-steel shell, and some discussion I found in "the trades" which said that SUT automation is suboptimal, apparently because the best single-use sensors (pH, temperature, etc) are not good enough for fully automatic operation. Combined with 100% manual unpacking, setting, connect/disconnect, and teardown of bags, the single-use idea seemed very much at odds with the fully automatic plant that many propose.
Finally, the gamma sterilization industry is extremely strained right now--the cobalt supply is tapped, or at least promised to EV-makers. New production of Co-60 is barely keeping pace with attrition at existing sterilization facilities, and the industry is already in triage mode with respect to what healthcare/biotech equipment gets to go through gamma sterilization versus what can go through an alternate sterilization, like ethylene oxide. So a significant expansion in the supply chain of SUT would be out of the question today.
(Aside: yes, ATFs are incredibly expensive today and their price could be expected to come down with market volume, but it doesn't matter in the terms of my analysis. In my perfusion analysis, the perfusion devices contribute $10 out of $50/kg, and I assert an affordability threshold of $25.)
Dave Humbird @ 2022-03-24T14:26 (+4)
Given recent events, it is perhaps relevant to note that half of the nuclear facilities capable of turning Co-59 into Co-60 are in Russia. Cobalt supply issues are not easing up anytime soon.
Matthew Stork @ 2022-11-18T18:56 (+2)
I appreciate the response here and want to clarify my argument a bit. I totally understand that currently available SUT isn't sufficient to make cultured meat cost-effective. I'm mostly arguing against the notion that these problems are intractable. To your point about the difficulties with gamma irradiation, it seems likely that there could be a reasonable alternative to gamma irradiation for SUT sterilization. At the moment, pharma companies get by just fine using stainless steel for processes > 2kL, so there isn't much pressure to improve from that angle. If single-use is truly enabling for cultured meat, then that provides an impetus for more investment in improved sterilization technologies.
The purported economic and environmental benefits of SUT are related to the elimination of sterilization steam (because everything is gamma-sterilized before shipping) and the elimination of cleaning chemicals (because the bags are not cleaned for reuse).
The major cost savings I see for a cultured meat plant would be in a reduction in the requirements for air quality. A fully single use plant with completely aseptic connections can (in-theory) be run aseptically without a clean room. There would just be a small clean room for media and solution prep. Existing pharma plants using SUT tend to still need high quality air as there are some steps in the process that require manual manipulation. I've seen it suggested though that future biopharma processes which use fully integrated and continuous systems can be run in clean rooms with drastically lower air quality than existing plants.
Combined with 100% manual unpacking, setting, connect/disconnect, and teardown of bags, the single-use idea seemed very much at odds with the fully automatic plant that many propose.
Moving to long duration perfusion (> 30 days) reduces the need for unpacking / teardown. There have been biopharma companies which have demonstrated the ability to run stable perfusion for up to 60 days. For the most part, companies haven't gone longer than that mostly because it's not really necessary.
Linch @ 2021-10-05T21:01 (+2)
Thanks a lot for your expertise and notes here! For context, how expensive are the single-use bioreactor bags? Both right now and realistic projections 5,10,20 years out?
I'm wondering to what extent this is something where the costs would seem very cheap for biopharma applications but too expensive for a commodity.
The internet claims about $30K for a 1K L bag, do these numbers seem approximately right to you? If so, how amenable are costs to >10x decreases?
Matthew Stork @ 2021-10-07T23:20 (+1)
Having never purchased a SUB myself, I don't know the exact cost, but $30k for 1000L bag seems ballpark correct for biopharma. That all said, it's just a big 'ol plastic bag, I would bet that a food-grade version could be at least 10x cheaper.
Looking at the materials (Single-use bioreactor - Wikipedia), these are all very typical polymers that should be quite cheap (in theory at least). You could get away with food grade plastics, which should be significantly cheaper than pharma grade.
SUBs have also only become popular relatively recently. My major biopharma employer only started using SUBs in a significant fashion in the last decade. My point being, I bet there is still room for improvement in manufacturing costs since SUBs are a relatively recent innovation.
Just to hedge a bit, it's a bit hard for me to give you exact numbers here in terms of how much room for improvement there truly is. I'm not a materials scientist and don't have intimate knowledge of SUB construction. It's entirely possible there is some super expensive step required to make those things, that just can't feasibly be reduced.
Neil_Dullaghan @ 2021-10-01T07:26 (+11)
Fwiw, the Good Food Institute have produced a "Statement addressing techno-economic analyses" and a "Preliminary review of technical assumptions within the Humbird analysis"
nil @ 2022-07-11T13:39 (+9)
Thanks for linking to GFIâs posts (and for your and Linchâs article in the first place!). GFIâs concerns w/ some of the points made in the TEAs and the Counter article seem sound to me (FWIW, as I have only some basic knowledge of the field at best). I couldnât find any responses to GFI, unfortunately.
For those who might be interested in checking GFIâs posts, below are some excerpts.
From the overview of âPreliminary review of technical assumptions within the Humbird analysisâ:
... [Humbird's] analysis is valuable for identifying and prioritizing areas where additional innovation is needed to overcome the current limitations. However, this analysis incorporates several assumptions and interpretations and that we feel merit further discussion or fail to acknowledge the current state of the science (e.g., where researchers or companies are already developing promising technologies that address said issue). We have enumerated several of these points below, in the hopes of providing clarity on some of the nuanced reasons that different TEAs reach different conclusions at this speculative stage of development of this emerging technology.
From âStatement addressing TEA analysesâ:
... the Humbird analysis, relying only on publicly available data, necessarily draws insights from the existing literature on parallel fields such as biopharma and cell therapy. The CE Delft analysis [commissioned by GFI], on the other hand, is the only publicly available techno-economic analysis we are aware of that uses actual data submitted by companies producing cultivated meat and its inputs, shared under NDA directly with the CE Delft team (not shared with GFI). Furthermore, all of the techno-economic analyses published to date only reflect challenges of pursuing scale-up of cultivated meat in fed-batch and perfusion-based stirred-tank reactor systems, which by themselves represent some of the methods that cultivated meat manufacturers are currently pursuing but do not necessarily represent the full range of [potential future] scale-up (e.g., here) or biomass-generating methodologies ... (e.g., here and here).
Modeling a process on public data from parallel but distinct cell culture processes that are also necessarily out of date (biopharma companies are typically not publishing their most recent innovations on process or cell line improvements, preferring to retain them as intellectual property) will lead to a muddled understanding of the state of the art, which can be particularly misleading in such a rapidly-progressing field.
As just one example relevant to the all-important questions of density and sterility, ... process intensification via innovations in bioreactor design, media formulation, and a shift toward continuous perfusion processes is now enabling densities 10- to 100-fold greater [than ~ 3Ă106 cells/ml] and with sufficient contamination control measures to allow for production runs that last weeks or months rather than days. These advances are only starting to be rolled out commercially in the last few years, and they are still mostly kept close to the vest within biopharma companies ... because of the enormous competitive advantage they confer.
Acknowledging areas where novel solutions may arise is not the same as naĂŻve or wishful thinking. There are some areas where true constraints, dictated by the laws of physics or thermodynamics, forbid workarounds. But for many of the core challenges facing the cultivated meat field, the search for alternate solutions is still in its infancy â we have far from exhausted the creativity of researchers in this field.
ââIn the [pharmaceutical] ... industries, cell biomass is essentially a waste product. ... For production of cultivated meat, the goal is to increase biomass while reducing the production of secreted proteins and metabolites. Optimization of cell lines for this purpose will therefore have opposite goals compared to all commercial animal cell processes in the past.
One option is to assume that animal cell culture is not feasible for large-volume, low-cost applications simply because it has historically not been used as such, but retrospectives tend to serve as poor barometers of the prospects for future innovation. A more forward-looking interpretation is that there is a tremendous amount of low-hanging fruit for relatively low-effort, high-impact process improvements guided by the new incentives and considerations under which the cultivated meat field operates.
⊠one could argue that the cell culture industry until now has actually been pushed toward higher costs than are necessary even at the current scale at which it operates, simply because of the âarbitrarily high margin[s]â it can capture. ⊠current prices reflect the realities of the current business model, market incentives, and risk tolerances more than they reflect true manufacturing or technology costs.
Even at small volumes and high price points, many cultivated meat companies will be able to find a scaling foothold that simply doesnât exist within commodity fuels and chemicals. ⊠A better comparative industry would be the plant-based meat industry, which is theoretically also competing with mostly-commoditized, massively-scaled incumbents but has proven capable of commanding several-fold higher price points ⊠.
Hybrid [ie plant-based X cultured meat] products could offset the high production costs of animal cell cultivation with more affordable plant materials while competing on other important consumer metrics such as taste and sustainability.
In general, techno-economic analyses and the critical perspectives of scientific voices well versed in other fields add great value to the cultivated meat industry by highlighting several key areas for further empirical and modeling research to validate assumptions and improve upon the limitations identified.
The article concludes:
It is far too early to write off cultivated meat based on early analyses that do not examine the full range of future possibilities. To the contrary: given what is at stake, we cannot afford not to invest significant resources in affording cultivated meat the greatest chance of success.
JuanGarcia @ 2021-09-29T11:50 (+10)
I found this really interesting:
Humbird first models a Techno-Economic Analysis (TEA) where all parameters are similar to bakerâs yeast [...] The analysis comes to $3.87/kg of wet (70% water) cell mass for the constrained yeast process. As yeast production at scale is already a highly optimized process over many decades, and the additional constraints mentioned so far are pretty close to the fundamental biological nature of animal cells, it seems unlikely that we can do better than a lower bound of $3.87/kg. Unfortunately, there are other constraints.
If you believe this analysis to be representative of reality, then it follows that cultured meat will never be able to reach parity with current chicken and pork meat prices. Together, these two make over 2/3 of global meat production.
See: https://www.indexmundi.com/commodities/?commodity=pork&months=120 https://www.indexmundi.com/commodities/?commodity=chicken&months=120 https://ourworldindata.org/grapher/per-capita-meat-consumption-by-type-kilograms-per-year?country=~OWID_WRL
Linch @ 2021-09-29T19:48 (+8)
If you believe this analysis to be representative of reality, then it follows that cultured meat will never be able to reach parity with current chicken and pork meat prices. Together, these two make over 2/3 of global meat production.
Yeah, and it's an even larger ratio from a moral perspective, at least if we are focused primarily on farmed animal welfare.
Of course, 1) just replacing beef is more than enough for a solid business case, 2) you can also try replacing really high-end luxury foods (Kobe beef, caviar, foie gras), where the lower bounds here don't apply, and 3) as you allude to, chicken and pork meat prices may increase.
(1) and (2) are more relevant for justifying cultured meat use from a business perspective than from an altruistic perspective.
3) is something I've seen many cultured meat proponents say, but of course we can't rely on it (for starters, chicken and pork meat prices might also decrease). That said, a moderate possibility that chicken and pork meat prices might increase ought to be sufficient to justify altruistic cultured meat investment, assuming that we can get prices close to parity with conventional meat prices. So 3) is unlikely to be a crux, within reasonable ranges.
JuanGarcia @ 2021-09-29T14:09 (+3)
Then again, I do believe that you can culture simple cells for a lower cost. I estimated the cost of producing protein-rich single cells from methane at $1-2/dry kg. https://osf.io/94mkg/
However, those numbers are for a bacteria that feeds on gas. The yeast analogy is much closer to mammalian cultures.
Linch @ 2021-09-29T17:58 (+3)
Oh very cool! I know you/ALLFED is focused on bacterial SCPs from the perspective of feeding earth after disasters, but do you have a quick sense of why we can't have it during normal times? Like what are the relevant timelines/bottlenecks against using bacterial SCPs as a way to partially replace animal agriculture?
Also more broadly did you do any BOTECs to look at the cost of yeast SCPs in comparison to bacterial SCPs? Just generally curious if we actually expect bacterial SCPs to have cost savings over yeast (waving away scientific problems)!
JuanGarcia @ 2021-09-30T12:59 (+2)
Pretty much the only thing currently standing between us and bacterial SCP-based food (such as from methane or CO2/H2) is the lack of approval for use as a human food. Most or all of these companies have shown interest in the human food market, and a few of them are publicly pursuing it, such as Solar Foods. I expect they will be available in the next few years.
As Humbird mentions in the TEA and other sources confirm, the production cost of baker's yeast is well known (~$1.80/kg dry), so no need to run any numbers for that. I'm fairly confident SCP from methane will be lower cost at scale as I mentioned above, but not SCP from CO2. Methane SCPs will almost certainly be quite a bit cheaper than yeast in terms of cost per unit of protein.
Fun fact: these protein-rich SCPs will be so much cheaper than cultured meats, that SCP companies have been promoting their use as a raw material for cultured meat production.
Linch @ 2021-09-30T22:04 (+3)
As Humbird mentions in the TEA and other sources confirm, the production cost of baker's yeast is well known (~$1.80/kg dry), so no need to run any numbers for that
I think there's two missing steps here.
1) yeast SCP for vegan meat replacement(Quorn) probably has importantly different processes and structure to baker's yeast. So I'm interested in whether it's realistic to expect ~$2/kg for that as well.
2) Humbird's TEA for yeast has both internal validity and empirical validation, and also he made a yeast TEA as a validation step to demonstrate that his model can retrodict an existing system. The secondary reason I asked for you to share the same methods that you've used for bacterial SCPs to get to yeast SCP numbers is so we can help make sure you aren't skipping calculation steps.
(But it's probably not worth you doing additional work here if you haven't already done so, just for my curiosity)
JuanGarcia @ 2021-10-01T10:41 (+5)
I think I see what you're getting at, let me add a couple of things:
- Quorn's mycoprotein is produced from a different microorganism (Fusarium Venenatum), with different growth rates and processing steps than baker's yeast (Saccharomyces cerevisiae), so you are correct. It is more expensive than yeast, and also compared to the gas-based SCPs I mentioned.
Based on a conversation I had with an ex-Quorn scientist, the wholesale selling price of Quorn products is ~$3/kg wet (which makes sense given the intensive postprocessing and other additional steps). I'm uncertain as to how it would differ from yeast when comparing them in a similar state (e.g. drying as pretty much the sole post-processing step, which is the case of the values I gave for yeast and methane-based SCP), but I imagine that even then Quorn would be at least twice the production cost of yeast/methane SCP.
- A little clarification about my research: I did not run a TEA as such to calculate capital and operational expenditures of the gas-based SCP production systems. Rather, I used published values from TEAs run by SCP companies themselves as an input to my model. I used these for my goal of estimating the retail price in a catastrope and the ramp-up speed of fast construction of SCP factories in case of catastrophe.
I did not try to perform validation of the published values as I did not have access to the calculations run by those companies. Instead, I made sure that my results are robust to relatively large changes in the TEA results published by the SCP companies via sensitivity analysis. I'm happy to talk more about the methodology if you're interested.
Stijn @ 2021-09-30T13:33 (+6)
I would expect that cultivated meat can reach price parity with animal-based meat, based on 'first principles'. Assume that all biological functions in an organism can be replicated with technologies, and that these technologies can reach the same efficiency as the biological functions that reached high efficiency due to evolution and natural selection. That is a realistic assumption, because no laws of nature have to be violated. To grow muscle tissue, we need oxygenation, so we invent a technology, call it 'lungs'. We need nutrients (amino-acids, sugars,...), so we invent a technology called 'intestines' to produce nutrients (e.g. from plant-based sources). If these new technologies are as efficient in doing what they have to do as their organic counterparts in animals, the production costs of cultivated meat and animal-based meat will be the same. However, using animals to produce muscle tissue is not maximally efficient, because of two reasons.
- The animal wastes resources (nutrients, energy) on unnecessary organs, tissues and body parts, such as brains, eyes, ears, tails, feathers, pain receptor cells, reproductive organs, hooves,... All these things are not necessary to grow muscle cells. Assume that these unnecessary body parts use 10% of nutrients and energy. Then a production unit (e.g. bioreactor) that does not use these body parts can be 10% more efficient and hence 10% less costly.
- Using an animal to harvest muscle cells, the many other body parts that are necessary for muscle growth, such as the lungs (for oxygenation), intestines (for production of the growth medium), skin (for thermal isolation and protection),... need frequent replacement when the muscle cells are harvested, because these body parts are destroyed (in the slaughterhouse). It is like using a bioreactor to grow cultivated meat, and after each batch, we destroy the whole equipment, including all sensors, tubes,... And then we built a new bioreactor (using a factory we call 'uterus'). That is not efficient, and very costly. I expect not having to construct a new production unit after each production cycle, will make cultivated meat production much more efficient (and hence less costly) than animal-based meat. Assume the production unit for animal-based meat (the necessary body parts, such as the lungs, intestines,... of the animal) consumes 50% of resources for its construction (growth), not having to construct so many production units could save almost 50% of resource use and hence costs.
So I expect with sufficient research, it is only a matter of time when cell-based meat reaches price parity, and it can perhaps drop to 50% of the price of animal-based meat. Plus, I consider it unlikely that none of the technologies can become more efficient than their organic counterparts, because it is unlikely that the current design of an animal is optimal (meaning that the current animal would have reached the final stage of evolution and that none of its organs can be improved).
Linch @ 2021-09-30T21:52 (+7)
I think this is a good start. I do have some internal notes on why (I think) this is the wrong way to do first-principles reasoning, for reasons that I plan to elaborate on later. Can speed up/prioritize publication if you (or other readers) think this is important for your thinking or decision-relevant for you.
Stijn @ 2021-10-02T17:50 (+3)
Please sure do! That would be very interesting.
Neil_Dullaghan @ 2021-10-01T06:33 (+2)
Thanks for sharing your perspective.
The prediction "it is only a matter of time" has an effect on how to allocate EA resources depending on how long that matter of time is, even with additional resources going towards it, so I'd be curious what time period you'd assign for this and how you came to think that.
Even without having to construct brains, eyes, ears, tails, feathers, Humbird thinks it will still be very expensive at the moment since creating the immune system is so hard to create- so you need pharma grade standards with are expensive (one can disagree with this assumption or think eventually it won't be true, as CE Delft do, but I'd be interested in clearer reasoning as to why one thinks it's likely)
I'm not sure why you assume the production unit for animal-based meat consumes 50% of resources for its construction (growth)?
Stijn @ 2021-10-02T18:14 (+1)
Concerning "it is a matter of time": the only worry that I see, is that it would take so long to develop cultivated meat that in the meantime we would have already abolished animal farming (or decreased it to such a degree that cultivated meat has little additional value) because of e.g. plant-based and fermentation-based protein. But I consider that unlikely (lower than 10% likelihood). Oh, and even if humans would be all plant-based vegans by then, then we still have the many carnivorous animals (pets,...) who may benefit from cultivated meat. Hence, I think speeding up cultivated meat R&D remains very effective (high risk high impact), especially for animal welfare. It may be less effective for e.g. climate change, because reductions of greenhouse gas emissions need to occur soon (within 30 years). But cultivated meat offers a cheap carbon capture and storage method (reforestation of agricultural land that was used for livestock). And I think carbon capture is still worthwhile even over 50 years.
I would say 30-50 years for whole tissue cultivated meat to reach price parity with animal-based meat. But I have no clue whether I'm good at forecasting.
About the 50% consumption of resources: that was just an assumption, somewhere between 0 and 100%, close to what I think is the proportion of edible tissue mass to whole body mass.
Davidmanheim @ 2021-09-27T06:24 (+5)
Minor note; "...a factor of 4 increase in cell density means that the percentage of bioreactor volume that is now cells would increase from 17.5% to 70%, very close to sphere packing density limits."
Sphere packing density limits shouldn't be relevant for cells, which are not rigid - they can deform to squish together, unlike in the sphere packing problem. (The problem of getting nutrients distributed is a different issue, of course.)
Linch @ 2021-09-27T07:17 (+14)
Thanks for the comment! The tl;dr is that getting nutrients distributed is a closely related issue of "viscosity," where sufficiently thickly packed cells will have effectively ~0 fluid flow, and that the theoretical upper limit for cells (~infinite viscosity at ~0.65) is close to and slightly lower than sphere packing limits.
Below is some notes from being nerd-sniped by this comment, no guarantees that it's at all good or useful. (Note that I certainly didn't know things to that level of granularity before your comment, so it was helpful for you to do this spot check!)
-
I agree that sphere packing is a simplifying assumption, as cells are both deformable and not spheres. However, it's not a crazy one to start with, and I think the practical bounds are much lower.
The problem of getting nutrients distributed is a different issue, of course
Actually, a closely related issue is viscosity, or how difficult it is for fluids to flow through something. The theoretical upper bound is when viscosity approaches â, where you can't get any nutrients at all.
My impression is that the question of the theoretical upper bound of packing with soft objects but other constraints like shear in a viscous solution has been one that interested CHO scientists and other people for over a century, arguably starting with literally Einstein.
Humbird uses Ïmax=0.65 as the theoretical upper limit for soft spheres as footnote 35 on page 14, citing a PhD thesis. The thesis lays out the problem pretty cleanly (emphasis mine):
There must come a time, as more and more particles are added, which gives continuous three-dimensional contact throughout the suspension, thus making flow impossible, i.e. the viscosity tends to infinity. This will be also correlated with the existence of the yield stress discussed later.
The volume fraction at which this happens is called the maximum packing fraction # and its value will depend on the arrangement of the particles. Maximum packing fractions thus range from approximately 0.5 to 0.75. The maximum packing fraction, as well as being controlled by the type of packing, is very sensitive to particle-size distribution and particle shape.
The thesis then gives the relevant numbers in pg 81-82:
As in the case of suspensions, we define a maximum packing fraction # (which is usually 0.64 or even 0.74 for solid spheres in a face-centered-cubic crystal), depending on cell elasticity, i.e. their compactness [Quemada 1998]. Due to the presence of soft spherical cells, it is expected that the value of # will be in this range. # is determined using the reduced viscosity plot as a function of ( at a shear rate of 10 2 s -1 , = 0.0013 Pa.s the solvent viscosity). In our case, this data is found to match the well-known equation proposed by Krieger and Dougherty [Krieger 1959], this providing the value # = 0.65 (Fig. 4.5).
The surrounding thesis has a lot of science that I don't feel confident in evaluating, and math that I think (perhaps arrogantly) that I am capable of evaluating, but (unfortunately) like many other problems I've encountered in this project, I chose not to.
Obviously I think there's a reasonably high chance that numbers from a random PhD thesis might be wrong, though I'm somewhat comforted by other lines of attack (including sphere packing) that bounds it at similar numbers . That said, my best guess is that small disagreements here will not change anybody's bottom-line cause prioritization of cultured meat, though perhaps it might be sometimes relevant for cultured meat implementation.
Stijn @ 2021-09-29T20:57 (+6)
What is the packing density of muscle cells in muscle tissue (meat)? Why not use that packing density as an estimate for the maximum possible packing density of muscle cells in a bioreactor?
Linch @ 2021-09-29T21:45 (+2)
This is a good question. I don't know how high the packing density is in muscle tissue, but I assume it's very high.
Note that the theoretical model of bodies and bioreactors are pretty different, e.g., bodies are much more structured and the problems of creating muscle cells and creating the scaffolding for such cells is coupled within the human body.
AFAIK, almost all attempts to make cultured meat is trying to solve the "create cell slurry" problem first and worry about scaffolding later, nobody (and this might be betraying my ignorance) is trying anything like making artificial fascia that grows contemporaneously with muscle cells in a bioreactor.
I'm not entirely sure why, I assume there are strong technical reasons that I don't (yet) know for this.
david_reinstein @ 2025-01-06T19:59 (+4)
By the way, you wrote "we also plan to hire external experts to red-team our analysis and check for relevant flaws post-publication."
Did you ever implement that?
Misha_Yagudin @ 2021-12-13T13:41 (+3)
An interesting outside view I stumbled recently concludes:
I think the typical pattern is for human artifacts to be 2-3 OOM less efficient than their biological analogs, measured by âHow much energy/mass is needed to achieve a given level of performance?â Manufacturing costs differ by a further 2-4 OOM.
Neil_Dullaghan @ 2021-12-13T19:21 (+2)
Thanks Misha. Can you share who the author of that document is? Looks like it might be Paul Christiano but I want to be sure.
Misha_Yagudin @ 2021-12-13T23:03 (+3)
I think he is the author.
david_reinstein @ 2021-10-04T22:22 (+3)
I made a 'Found in the Struce' podcast episode reading this, and making a few comments and suggestions. (I'll ask @dothemath to put this in the EA Forum Podcast too).
I also read the comments (with some summarizing).
It was a bit challenging for me because of my lack of biology background, but I made it through. Hope it's helpful to have the audio format.
Chriswaterguy @ 2022-06-03T23:28 (+1)
What's the story with Eat Just selling cultured chicken bites in Singapore â are they being sold at a loss, and/or does the product only contain a small amount of the chicken product?
https://www.straitstimes.com/singapore/more-cultured-chicken-products-approved-for-sale-in-singapore
I've read elsewhere that the initial version wasn't quite 100% vegan, but they later eliminated the need for fetal blood.
Charles He @ 2022-06-04T00:04 (+2)
What's the story with Eat Just selling cultured chicken bites in Singapore â are they being sold at a loss, and/or does the product only contain a small amount of the chicken product?
Here are some lines from the article:
They were sold at 1880 Singapore, a social club at InterContinental Singapore.
A private tasting session will first be held at JW Marriott Hotel Singapore South Beach next week.âOne thing Iâm worried about, though, is the price point, since it is manufactured in a lab. Hopefully, the meat will still be affordable to the public when it is sold in hawker stalls,â she added.
Someone I know has a "personal aesthetic, world view or ideology" that's absolutely ruthless and skeptical when it regards situations related to business and moneyâparticularly and especially when they are (conveniently) adjacent to "non-profit" narratives[1][2].
This ideology would read in between the lines of this article quoted above, and call these actions performative.
For example, this event is consistent with not having a viable commercial path and instead is trying to "get buzz" as part of a larger business strategy to support investment and interest.
This doesn't indicate anything positive about the feasibility of the product (especially in the context of substantial existing impartial analysis) and isn't an update.
- ^
Like, informed from decades of interactions with multiple instances of people in small businesses, non-profits, enterprises, big corporations, FANGs, e.g. working with the middle and upper management, marketers, from each of these instances
- ^
So the reason why this footnote and the above footnote exists is that this person specifically claims these experiences and model of the world is powerful and much faster than tracking down/interviewing/investigating, because they can read things almost immediately that are being telegraphed.
Charles He @ 2022-06-04T00:08 (+2)
I haven't heard or read anything about Eat Just's business or the founder before.
After writing the above comment, I found this Guardian article and read it for the first time:
https://www.theguardian.com/food/2021/jun/16/eat-just-no-kill-meat-chicken-josh-tetrick
The below are just straight from the middle of the article (bold is mine):
From the outset he showed a knack for raising capital but had a tendency to rapidly âblow throughâ the money he raised, says Javier ColĂłn, the original operations manager and third employee of the company. ColĂłn claims he tried to rein in the spending and Tetrick fired him; he says he has been a detractor of Tetrickâs leadership ever since.
The company gained early fame after it fended off a lawsuit from the food giant Unilever, who sued over the use of âmayoâ in the productâs name. By 2014, Tetrick had impressed investors by getting Just Mayo on to the shelves of major supermarkets including Whole Foods and Safeway.
But controversy hit when, in a series of 2016 articles, Bloomberg reported the company had instructed employees to buy up huge quantities of Just Mayo â sometimes 140 jars a day â in a scheme allegedly aimed at driving up revenues as Hampton Creek was seeking further investments. The company claimed it was only buying small amounts for quality control testing. Investigations by the Department of Justice and Securities and Exchange Commission were eventually dropped.
A former scientist at the company, who spoke to the Guardian on the condition of anonymity, confirmed similar details to those reported by Bloomberg, saying employees were called to an âall handsâ meeting and asked to buy out a storeâs entire mayonnaise stock, offering an explanation to store managers such as procuring supplies for a company picnic.
âThat sort of thing was pretty common. It was the way the place was run,â says the scientist, who adds that it wasnât unusual to see slide decks for prospective investors that overstated the companyâs capabilities, or to be asked to avoid disclosing the real facts to board members when they came to visit headquarters.
When employees complained about misleading practices, the scientist says âmanagers would just say: âThis is supposed to be aspirational. Itâs just marketing.ââ
By early 2017 nearly all the companyâs directors had resigned, leaving only Tetrick on the board. Bloomberg reported that the resignations followed months of infighting, during which directors and investors âlost faith in the aggressive founder theyâd previously hailed as a visionaryâ.
In a statement, Andrew Noyes, Eat Justâs spokesman, said the Bloomberg articles were based on false charges by disgruntled former staff.
Several other former employees say they did not find Hampton Creekâs practices particularly questionable, with one former manager describing its ethics as typical for Silicon Valley.
âI think itâs a normal Silicon Valley story of a company that was over-hyped and has lived through this rollercoaster of hype and scandal and now itâs just plodding along,â says the former employee, who asked not to be named because he signed a non-disclosure agreement.
âJosh is a normal Silicon Valley huckster. He stays on the legal side of the line. But he straddles that line,â he says. âItâs just like Uber. People keep saying itâs a house of cards and itâs going to fall down. But it just keeps standing.â
In response to criticism of his leadership, Tetrick says he is driven by an ambitious vision for the company, even if that vision has yet to be fully realized. âSome companies are going to take longer to get to profitability than others,â he says. âBut itâs really important that you have a path.â
....
Pelling believes that the problems inherent to lab-grown meat can someday be solved, but he worries about companies like Eat Just rushing to market with solutions that havenât been scientifically vetted or transparently explained to the public.
âMy concern is this could blow up at some point,â says Pelling, âAnd what might have been a real solution â maybe not the whole ecosystem, but maybe part of it â might never happen, because trust gets destroyed and wiped out.â
Linch @ 2022-06-03T23:44 (+2)
It's a good question. In 2021, we tried tracking the 1880 Eat Just chicken nuggets and they were actually quite elusive. (supposed to be only sold only once a week, and then only available online at a specific time of day, and then our contractor in Singapore couldn't get access to it after trying for two weeks).
I haven't followed the space since. Would be excited to see other people comment.
FGH @ 2021-11-11T14:34 (+1)
Hi all, adding a (refreshingly appreciative and rational!) update from the people who made the first cultivated meat burger in 2013, for reference : https://mosameat.com/blog/cultivated-meat-progress
Linch @ 2021-11-14T01:46 (+4)
I skimmed it and didn't learn anything new, and my best guess is that reading that post would be anti-informative in the sense of giving people a worse Brier score if they were asked relevant questions about cultured meat.
Can you illustrate parts of it that you think are unusually rational/informative? (Note that this is an honest question, as I skimmed it very quickly)
Stijn @ 2021-10-07T14:14 (+1)
One more addition to the cultivated meat feasibility discussion: https://stijnbruers.wordpress.com/2021/10/07/the-crux-of-the-cultivated-meat-feasibility-debate/
I argue why we have to make a distinction between the functions (e.g. taste, nutrition,...), the products (e.g. muscle-based meat, plant-based meat) and the production processes (e.g. animal-based meat, cell-based meat). I expect that cell-based meat is feasible (can reach price parity with animal-based meat), but that we are uncertain about the time frames for innovation (of cell-based meat) versus substitution (towards plant-based meat). Given these considerations, cell-based meat research and development has to be considered more like an insurance policy.
david_reinstein @ 2021-10-04T22:27 (+1)
Main comments/suggestions:
-
I donât know what most of the biology terms mean. Maybe you should link this to âa primer on the biology of cultured meat etcâ?
-
Iâd also like to better understand the methods used in these analyses in terms of the statistics/data sci/economic stuff. Like
-
what are these â9 parameters that become 4 factorsâ in the third paper?
-
How do their estimates and ranges work? Are they incorporating uncertainty in Bayesian/Fermi-Monte-Carlo-ish ways?
-
Future work could be done in the context of an explicit overall calculation/guesstimate, with interactive visualizations to help us understand how each factor affects the total cost estimate
-
What would be nice would be to be able to have a sort of âproduction functionâ for cultured meat depicted and explained somewhere.
- Which are fixed costs
- Which things add
- which things multiply
- which are substitutes in the process
- what are the physical constraints, etc.
Some of this may be out of the scope of an EA forum post, but this question is so important that we should not be limited by this format IMO.
Linch @ 2021-10-04T23:28 (+3)
I donât know what most of the biology terms mean. Maybe you should link this to âa primer on the biology of cultured meat etcâ?
I'm not aware of any really good primers. For what it's worth, I've usually found the first page of Google search to be sufficient most of the time, and if not, pinging my biologist friends with targeted questions is sometimes useful. Of course, this might be too high a bar to reasonably expect for someone who's only reading our summaries; Neil and I will consider whether it's worthwhile to make a good vocabulary list.
I still don't know what all the terms in cultured meat means, and sometimes in practice what ends up happening is that I treat terms like what Scott calls "crenulate their zeugma"as placeholders and I just cross my fingers and hope it isn't actually that important. (I genuinely suspect they aren't, for what it's worth).
A bigger problem with a lack of understanding, to me, isn't the terms but the underlying scientific details. cf Feyman's quote. Unfortunately I don't have a good way around this.
Iâd also like to better understand the methods used in these analyses in terms of the statistics/data sci/economic stuff. Like
I'll let Neil answer about the Risner (third) paper specifically, but the short answer is that I don't think the treatment of statistics or probability in any of these papers is particularly impressive.
Future work could be done in the context of an explicit overall calculation/guesstimate, with interactive visualizations to help us understand how each factor affects the total cost estimate
Yeah agreed. I think a really good TEA that would be very useful for EA folks would require someone or a team of people to have the following:
- A deep understanding of the scientific, engineering, and economic problems involved
- A commitment to truth-seeking, high rigor, and no "axe to grind"
- A reasonable formal or intuitive understanding of probability and statistics.
Unfortunately, the existing analyses so far only has 0-2 of the above. Neil and I are likewise missing #1 on this list (I'm sure other people may contest whether we have #2 or #3 as well!)
Re
What would be nice would be to be able to have a sort of âproduction functionâ for cultured meat depicted and explained somewhere.
Yeah I can see how this will be valuable. The Hughes review also complained about under-specificity. The main problem with such an approach is that it's hard to have a very precise production function for a futuristic technology (which GFI also complained about), though Humbird is the best treatment we're aware of on that topic.
david_reinstein @ 2021-10-08T21:04 (+1)
Thanks. This
Iâd also like to better understand the methods used in these analyses in terms of the statistics/data sci/economic stuff. Like
I'll let Neil answer about the Risner (third) paper specifically, but the short answer is that I don't think the treatment of statistics or probability in any of these papers is particularly impressive.
Makes me think your pessimism might be premature, in the absence of clear and strong evidence?